NCSF Thick Plate Uncoiler Straightening Feeder 3 In 1 Machine Applicable Plate Thickness: 0.6mm~6.0mm
Advantages
-
PLC control
-
Servo motor drive
-
Numerical control
Product Description
· 3 In 1 NC Servo Straightener Feeder W/Uncoiler
To optimize looping space and enhance safety, the coiled material travels from the uncoiler, guided by advanced photo sensors through left and right free guide rollers, allowing for efficient looping. As it progresses downward, it passes through the opener device and bending roller system, facilitating smooth downward feeding. This journey includes checkpoints such as the opener device, coil tip flatness device, pinch rollers, work rollers, and feed rollers, ensuring a seamless and controlled feeding process for the coiled material.
· STANDARD ACCESSORY:
1. Electric Eye Loop Control System
2. Hard Chrome Plated Feed and Straightener Rolls
3. Hold Down Arm Device
4. Advanced Worm Gear Screw Jacks for Easy Feeding Line Adjustment
5. Inverter-Controlled Uncoiler
6. Pneumatic Threading Tables at Uncoiler and Straightener
7. Hand-Set Coil Width Guide at Outlet Side
8. Hand-Wheel-Adjusted Coil Width Guides at Straightener Inlet Side
9. Reference Indicator Adjuster
10. Coil Tip Flattener
11. Air Disc Brake Equipped Uncoiler
12. Coil Keeper
· OPTION:
LIHAO’S coil car
Shearing device
· Features
1. Streamlined Operation: All feeder functions are consolidated within the PLC and a portable knob, simplifying control without overwhelming the operator with excessive function keys.
2. Enhanced Efficiency and Safety: By replacing manual operation with mechanical action, unnecessary time is minimized, boosting work efficiency while ensuring operator safety. The feeder offers a plethora of auxiliary functions for material feeding and support, allowing operators to maintain a safe distance from the materials.
3. Versatile Control Options: Users can seamlessly switch between punch master or device master modes based on their requirements, enhancing device adaptability and reducing costs.
4. Optimal Footprint: Despite the powerful capabilities of the Lihao NCSF series, its form factor remains the most reasonable in the industry, maximizing site cost efficiency.
5. Robust Control System Compatibility: Utilizing a comprehensive set of Japanese Mitsubishi control systems, the NCSF series ensures compatibility with various domestic and international standards, eliminating concerns regarding data conversion and enabling direct operation.
6. Thoughtful Design: Pioneering industrial design in the industry, the NCSF series prioritizes equipment visibility and operational comfort while maintaining fundamental performance standards.
· Structure
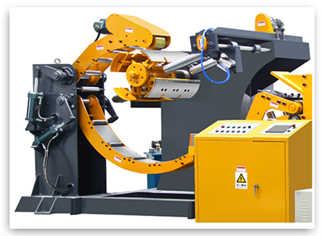
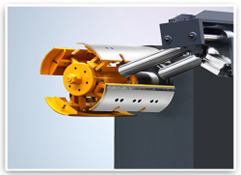
· Material part
The frame component of the material frame is meticulously welded using Q235B steel, prized for its elongation, strength, and weldability, making it a staple in general mechanical parts manufacturing. Laser cutting ensures the flatness of the entire plate, followed by CNC machining for precise hole positioning. Afterward, CO2 protection welding secures the rack's size integrity. Subsequently, annealing heat treatment enhances the steel's internal structure, maximizing its performance potential. This heat treatment process not only strengthens the metal, reducing structural weight, but also elevates mechanical product quality and significantly extends machine part lifespan. Additionally, it eradicates welding-induced defects, eliminates segregation, reduces internal stress, and promotes uniform steel structure and properties.
· Material spindle
The spindle bearing bore is precision-crafted using a horizontal boring machine, ensuring coaxiality below 0.015mm. Crafted from 40Mn tube forging, the main shaft of the material frame undergoes spheroidizing annealing, quenching, and tempering treatments. These processes significantly enhance the main shaft's flexibility, surpassing that of common carbon steel pipes typically used in the industry. This enhanced flexibility maximizes the spindle's load-carrying capacity, resulting in smoother coil starting and stopping while reducing motor load.
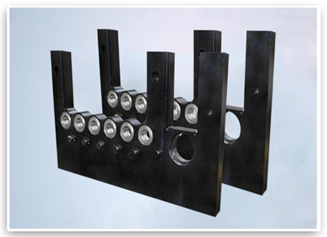
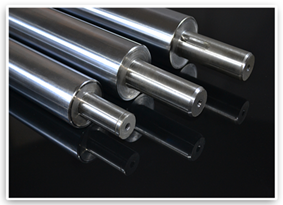
· Left and right vertical board
The left and right vertical plates of the straightening head are constructed from ZG25 cast steel, prized for its high strength, excellent plasticity, toughness, and welding performance, ensuring minimal deformation and exceptional stability. Each set of equipment undergoes a meticulous manufacturing process: the left and right vertical plates are precisely formed using molds and cast from ZG25 steel. Subsequently, annealing exposes the material to high temperatures for an extended period, followed by slow cooling. This annealing process serves multiple purposes: it addresses various structural defects and residual stresses that may arise during casting, forging, rolling, and welding processes, thereby preventing workpiece deformation and cracking. Additionally, it softens the workpiece for easier cutting, refines grain structures, and enhances mechanical properties. Furthermore, CNC pair processing ensures the accuracy of the vertical plate holes, ensuring stability and reliability.
· Correct roller part
The correction roller serves as the cornerstone component of the Uncoiler, Straightener, and Feeder 3-in-1 system. Lihao Machinery employs a sophisticated processing technique for this critical part: GCr15 round steel is forged and undergoes pre-heat treatment, including spheroidizing annealing. Following this, a series of precision procedures ensue: carburization, milling, intermediate frequency treatment, coarse grinding, and deep cooling. Subsequently, a refining process is applied, culminating in a plating finish. This meticulous process ensures maximum accuracy, concentricity, surface finish, and hardness, thereby significantly extending the lifespan of the correction roller.
· Gear section
The gear machining process at Lihao Machinery comprises gear grinding, tooth surface processing, heat treatment, and tooth surface finish grinding. Forged parts undergo normalization treatment to enhance cutting efficiency. Gears are designed based on drawings, followed by roughing, semi-finishing, carburization, rolling, and shaping. Heat treatment is then applied to enhance mechanical properties. Final steps include finishing, benchmarking, and tooth profiling. This process yields gears with a grade of 6, boasting high wear resistance, strength, and longevity.
· Specification
Model | Unit | NCSF-400A | NCSF-600A | NCSF-800A | NCSF-1000A |
Material width | mm | 100-400 | 100-600 | 100-800 | 100-1000 |
Material thickness | mm | 0.8-6.0 | |||
Maximum material weight | Kg | 3000 | 5000 | 5000 | 7000 |
Roll inner diameter | mm | Φ508 | |||
Roll outer diameter | mm | Φ1050-Φ1600 | |||
(For outer diameters less than 1050, please specify in advance) | |||||
Correction roller | pieces | 7 pieces Up 4/Down 3, diameter 68MM | |||
Feeding roller | pieces | 2 pieces Up 1/Down 1, diameter 84MM | |||
Feeding roller | pieces | 2 pieces Up 1/Down 1, diameter 84MM | |||
Air pressure | Mpa | 0.55-0.60 | |||
Servo motor | kw | AC 5.5 | AC 7.5 | ||
(Add a two-stage transmission system to increase output torque) | |||||
Rack motor kw | kw | AC 2.2 | AC 3.7 | AC 5.5 | |
The height of the feeding line | mm | the customer requires ± 100 (important parameter, to be filled in by the customer) | |||
Feeding accuracy | mm | When 0-400,±0.2 | When 0-600,±0.2 | When 0-800,±0.2 | When 0-1000,±0.2 |
Expansion range | mm | Φ460-Φ530 | |||
Expansion method | Hydraulic expansion | ||||
Feeding direction | from left to right/from right to left (important parameter, to be filled in by the customer) | ||||
Using materials | Hot rolled plate, cold-rolled plate, pickled plate, stainless steel | ||||
Working power | AC380±10%,50HZ,three-phase five wire system | ||||
Machine color | according to catalog (host RAL9010), yellow for protective and movable parts |
yield point stress(N/mm²) | 245 | 368 | 490 | |
tensile strength(N/mm²) | 392 (40kgf/mm²) | 488 (50kgf/mm²) | 580 (60kgf/mm²) | |
thick plate(mm) | 2 | 400 | 400 | 398 |
2.5 | 400 | 400 | 319 | |
2.8 | 400 | 379 | 285 | |
3.2 | 400 | 332 | 250 | |
4 | 400 | 266 | 200 | |
4.5 | 360 | 240 | 180 | |
5 | 290 | 193 | 145 | |
6 | 200 | 133 | 100 |
· Electronic control configuration table:
No. | name | brand |
1 | Reduction motor | Xinhua |
2 | Servo Motor | Yaskawa |
3 | Touchscreen | Weilun |
4 | PLC Programmable Logic Controller | Mitsubishi |
5 | circuit breaker | Schneider |
6 | contactor | Schneider |
7 | Control button | Hequan |
8 | relay | Schneider |
9 | Pneumatic components | Sanchi |
10 | Hydraulic Station | Chuanglibo |
11 | Photoelectric sensing | Omron |
12 | Cylinder | Sanchi |
13 | Leveling bearing | NSK |
14 | Frequency converter | Sanke |
15 | Servo Drive | Yaskawa |
· Applications
The NC Feeder is suitable for high-speed fixed rotor stamping production lines, heat exchanger stamping production lines, brake pad and friction sheet production lines, hardware parts stamping production lines, radiator production lines, new energy battery shell stamping line, and more.
· Package
Based on the specific characteristics of different products, packaging should be as follows, if necessary:
· Lihao Pre-sales Service
1. Custom 3-in-1 coil feeding line machinery: Based on the technical parameters of the application-related equipment provided by the customer, we can modify our machines to meet the customer's convenience and high production efficiency.
2. Solution Design: According to the customer's product processing requirements, we design unique solutions to support higher manufacturing efficiency and better processing quality.
· Lihao After-sales Service
1. As a professional manufacturer and supplier of automation machines, LIHAO provides English training videos and user manuals for uncoiler straightener feeder 3 in 1 coil feed line machines, covering installation, operation, maintenance, and troubleshooting. Additionally, we offer technical guidance through remote means such as TeamViewer, email, mobile, WhatsApp, Skype, and 24/7 online chat when you encounter issues with installation, operation, or adjustments.
2. Customers can choose to come to our factory for 2-5 days of training. We will provide professional guidance and effective face-to-face training.
3. Our engineers will provide on-site guidance and training services at your location. We will require your assistance in arranging visa procedures, prepaying travel expenses, and accommodating us during the business trip and service period.
· Lihao Automation Feeder Machine Guarantee
1. The entire coil feeder lines machine is covered by a 1-year free warranty.
2. Lifetime maintenance is provided, with our after-sales department offering 24/7 online support.
3. We offer machine-related parts services. After the 1-year warranty period, buyers will need to pay for repair parts.
· Shipping to Around the World
The uncoiler straightener feeder 3 In 1 machines can be shipped worldwide via sea, air, or express logistics through DHL, FedEx, and UPS. You are welcome to obtain a free quote by filling out the form with your name, email, product, and requirements. We will promptly contact you with complete information, including the most suitable delivery method (fast, secure, discreet) and shipping costs.